What are SEMI standards and what is their purpose?
The global industry association SEMI is a network organization for semiconductor, photovoltaic, electronics and other high-tech industries. It aims for collaboration to enable efficient and high quality, addressing the top challenges together. One component to reach these goals are the SEMI Automation Standards. They provide guidelines for fabhost and equipment communication and behavior to ensure seamless efficient interoperability and fast integration. These standards, agreed upon by suppliers and customers within these technologically highly demanding industries, are refined and updated regularly, meeting new industry requirements.
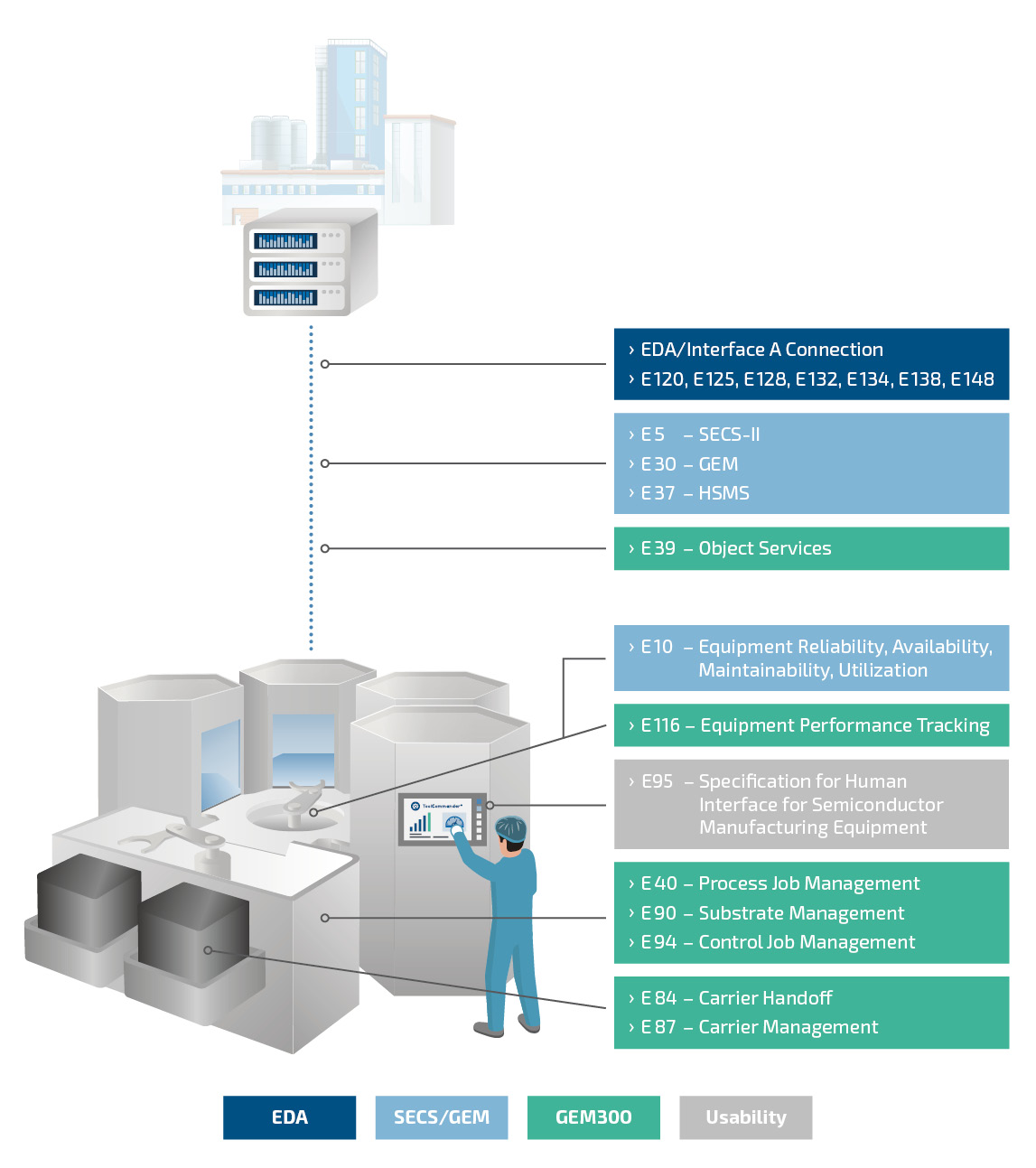
Different standards deal with particular tasks. While the SECS/GEM (SEMI E5, SEMI E30, SEMI E37) and EDA standards deal the equipment-host-communication, GEM300 standards address Carrier handling (SEMI E84, SEMI E87), Job Management (SEMI E40, SEMI E94) as well as Substrate Management (SEMI E90) within the production equipment. In doing so, they enable an even higher level of automation than the SECS/GEM standards already do. Dedicated standards for equipment performance tracking (SEMI E116) and basic equipment reliability data (SEMI E10) can give OEMs and fabs information on equipment efficiency. Visualization design standards like SEMI E95 ensure clarity and fast reaction capabilities when operating with the GUI.
SECS/GEM – Equipment-Host-Communication
The SECS/GEM standards lay the foundation for efficient equipment integration.
- The first layer is the communication protocol. While in former days, RS-232 communication (SEMI E4 – SECS-I) was sufficient, it is common practice today to use the faster TCP/IP connection (SEMI E37 – HSMS). This physical defines electrical and mechanical aspects of Ethernet communication, such as connectors or signal levels.
- In the second layer SEMI E5 – SECS-II, structure and content of messages to be sent are described. These messages, called “Functions”, are grouped in “Streams” by their purpose (e.g. job management).
- The third layer is the General Equipment Models (GEM). It provides the fab host with information of interest and describes expected equipment and host/MES behavior and capabilities (SEMI E30). This includes, e.g. remote control, publication of data, alarms and events, process program management (PPM) and state models.
This enables fast integration and communication without equipment and host/MES knowing details about each other. A thorough documentation of the equipment’s SECS/GEM connectivity interface is mandatory.
It is possible to use an equipment control that already has SECS/GEM communication capability or to equip an existing system with a SECS/GEM software solution such as FabLink®. FabLink® handles SEMI-compliant communication between a PC-based equipment control or a PLC system and the factory IT system. Various interfaces such as API, protocols and PLC-specific libraries are available for this purpose.
SECS/GEM Standards
- E4 – SECS I
- E5 – SECS II
- E30 – General Equipment Model (GEM)
- E37 – HSMS
- E116 – Equipment Tracking
GEM300 – SEMI standards for the fully automated fab
The fab you want to integrate your equipment to uses Overhead Transportation Systems (OHT), Automated Material Handling Systems (AMHS) or Automated Guided Vehicles (AGVs)? This is when the GEM300 SEMI standards come into play additionally to the SECS/GEM standards.
Enhanced traceability and job management requirements are necessary to orchestrate the production.
Carrier Management and handoff
SEMI E87 (Carrier Management) defines material transfer scenarios to load and unload Carriers with Substrates. On arriving at the equipment via an automated transportation, the CarrierID is read and validated to check whether the expected Carrier has arrived. Once the validation has been successful and the SlotMap has been read and validated, the material inside the Carrier is accessible and ready to unload.
Substrate Management
The SEMI E90 standard is essential for tracking the material on its way through the equipment. At all times, the position and status are known and can be called by the host.
Job Management
Jobs are used for tools with re-occurring, long-running or complex procedures. The two types of Jobs are Control Jobs (SEMI E94) and Process Jobs (SEMI E40). As soon as the expected material has arrived and accepted at the production equipment, a control job assigns the substrate to one or more Process Jobs, which contain the recipes that shall be used. The Process Jobs are scheduled to be performed in a specific order. It is possible to run several process jobs at once on an equipment. After starting the job, it can be paused, parameters can be adjusted (if authorized), resumed or aborted.
Fully automated fabs were first built around the time that 300 mm wafers were produced and processed. Transporting the bigger and thus more valuable wafers automatically from one equipment to the next had 2 main advantages: An ergonomic one for the individuals formally transporting the cassettes, and with regard to possible contamination.
The highest clean room class was only demanded in smaller closed areas (equipment and Carriers), which was easier to achieve and maintain. The wafer size made it into the name of the standard set. However, also 200 mm fabs may be equipped with this degree of automation and therefor apply the GEM300 standards.
If you meet GEM300 requirements, we, as experts, provide GEM300 requirements analysis, SECS/GEM and GEM300 training, consulting, SEMI interface implementation as well as commissioning and support.
Our SEMI compliant software framework ToolCommander® for equipment control and visualization as well as the field proven and well established connectivity solution FabLink® will comfortably make you skip the world’s semiconductor market entry barriers.
GEM300 standards
- E39 – Object Services
- E40 – Process Job Management
- E84 – Carrier Handoff
- E87 – Carrier Management
- E90 – Substrate Management
- E94 – Control Job Management
EDA (Interface A) – Sporting High-Volume Data to Improve Productivity and Quality
Equipment Data Acquisition is an additional interface, co-existent to SECS/GEM. It allows real-time monitoring on the host’s side and enables prompt issue identification. By having timely access to accurate data, EDA/Interface A empowers decision-makers to implement data-driven strategies for process optimization, quality improvement and yield-enhancement.
Key Components of Equipment Data Acquisition
- Common Meta Data: EDA/Interface A defines a common set of metadata, including equipment model with Equipment Self-Description, status, parameters, and events. This standardized metadata structure ensures consistency in data representation across different equipment types and manufacturers.
- Data Collection Services: The protocol supports various data collection services, such as periodic data collection, event-driven data collection, and conditional data collection. The creation of customized Data Collection Plans (DCPs) is possible. This flexibility allows host systems to retrieve data based on predefined triggers or conditions, enabling proactive decision-making and process optimization.
- Event Notification: EDA/Interface A facilitates real-time event notification from equipment to host systems. Events such as equipment state changes, alarms, and process deviations are communicated instantly, enabling rapid response and minimizing production disruptions.
- Error Handling: The standards include mechanisms for error detection and recovery to ensure robust and reliable communication between equipment and host systems. Error codes and recovery procedures are defined to address communication failures and data inconsistencies effectively.
EDA/Interface A standards
- E120 – Common Equipment Model
- E125 – Equipment Self-Description
- E128 – Specification for XML Message Structures
- E132 – Authentication and Authorization
- E134 – Data Collection Management
- E138 – Semiconductor Common Components
- E145 – Classification for Measurement Unit Symbols in XML
Providing secure Production Equipment: Cybersecurity SEMI Standards
The Cybersecurity SEMI Standards play a vital role in ensuring the integrity and security of semiconductor manufacturing processes. These standards provide guidelines and best practices for safeguarding sensitive data, preventing cyber threats, and maintaining the reliability of semiconductor production facilities. By adhering to the SEMI Standards regarding cybersecurity, manufacturers can bolster their defense against evolving cyber risks and uphold the trust of customers in the semiconductor industry.
Cybersecurity Standards:
- E187 - Cybersecurity for Fab Equipment
- E188 - Malware Free Equipment Integration
Easy Equipment Integration: SEMI Standards for Photovoltaic industry and Electronic Production
SEMI provides industry-specific standards for the PV industry and electronics manufacturing that are tailored to the respective requirements. This is a subset of the SEMI standards for the semiconductor industry. By standardizing practices and technologies from different manufacturers, they aim to improve efficiency, quality and interoperability.
PV and Electronics manufacturing Standards:
- PV2
- A3
Your contact person
